Photos and Text by Bill Lane
All materials, people, etc., had to be loaded at Sondrestrom (BW8) on the C130’s and flown to Dye 2 on the ice cap.
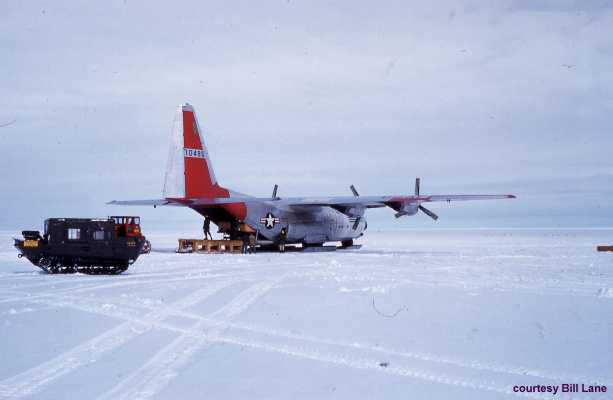
Note the ski-equipped landing gears.
The transportation of people and materials was a big deal on this project. For example, the structural steel was fabricated in the U.S. by American Bridge, shipped to a sea port, loaded on a ship, sailed to BW8, unloaded from ship, loaded on a truck, hauled to a the contractors yard, unloaded, separated for Dye 2 and Dye3, loaded on pallets (size and weight had to meet the requirements of the aircraft), pallets loaded on a truck (see photo below), pallets hauled to a C130, pallets loaded on the plane, aircraft flown to Dye2 and unloaded.
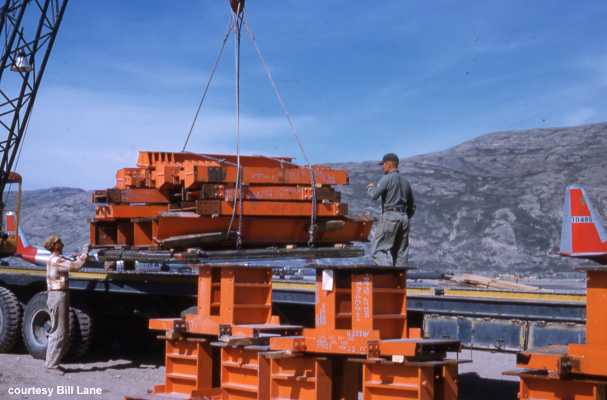
These photos show the building at various stages of construction.
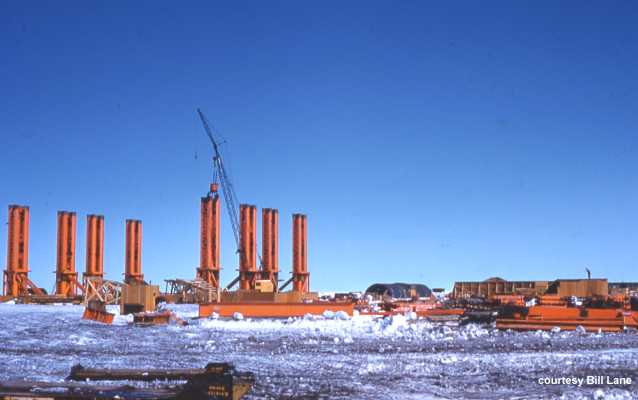
The main building columns are being erected.
The underground structure cannot be seen. The foundation consisted of a heavy timber mat founded on ice and a structural steel grillage founded approximately 30 feet below grade. The sixteen columns (8 pairs) shown in the photo, are supported on the grillage/timber mat. Each pair of columns is braced horizontally in both directions by a truss type framework. Note the horizontal frame around each pair of columns. Also note the sloping and vertical steel members framing into the bottom of the steel frame. The foundations and steelwork are protected by a timber enclosure. Note the exposed areas of the top of the timber enclosure.
Note the mechanism the crane is lowering between a pair of columns. It is part of the jacking system that could raise the building as new snow and ice accumulated at the top of the icecap. The system included sixteen 350 ton jacks.
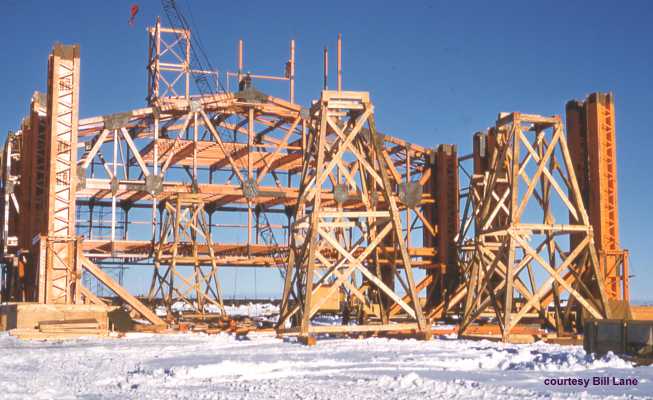
The structural steel erection continues. Note the timber falsework in the foreground that are used to support the main trusses during erection.
Note the horizontal frame at each pair of columns and the sloping and vertical steel members framing into the bottom of the steel frame. Note the exposed areas of the top of the timber enclosure.
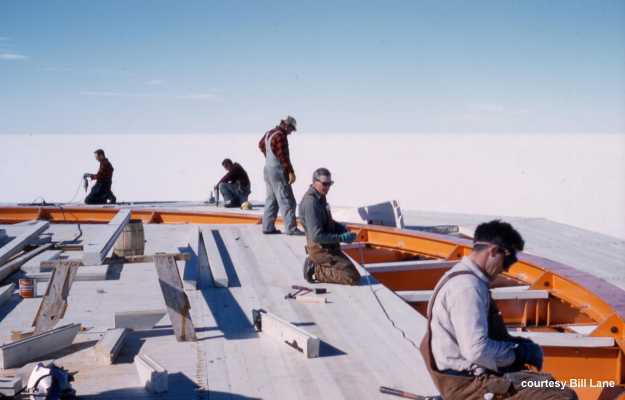
Heavy timber decking is being installed at the top level of the main building. Note the steel ring that will support the radome.
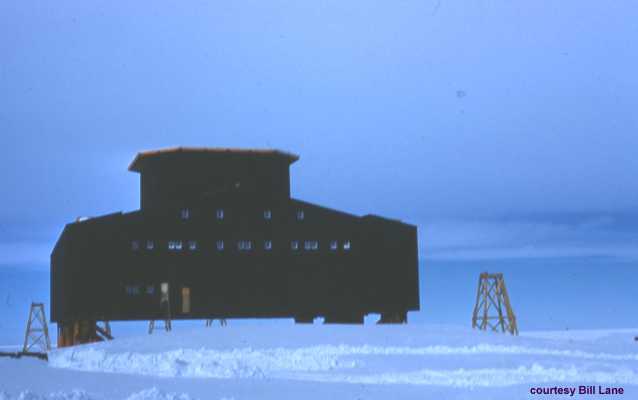
April, the beginning of the 1960 construction season. The job was shut down during the winter. Note the accumulation of snow.
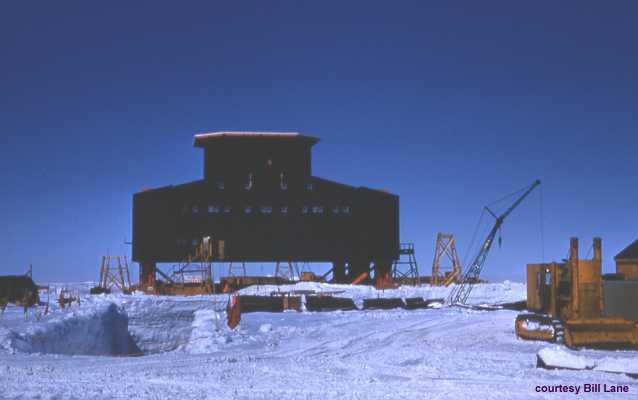
Note the excavation for the four underground P.O.L. storage tanks in the foreground. The tanks are under construction, note the crane boom projecting out of the excavation.
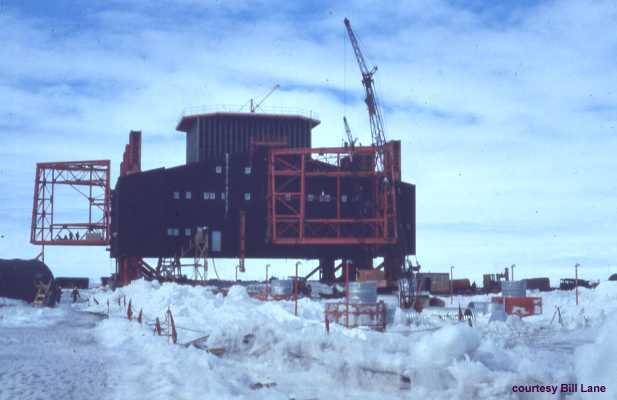
The lateral antenna enclosure structural steel is being erected. The main column extensions have been completed. Back fill has been placed around the four P.O.L. storage tanks. Note the corrugated metal pipe tunnel between the tanks.
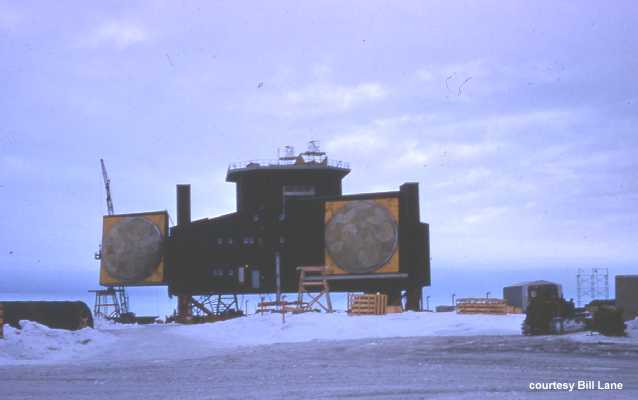
The lateral antenna enclosures have been completed. Note the outbuilding on the right and the vents from P.O.L storage tanks in the foreground.
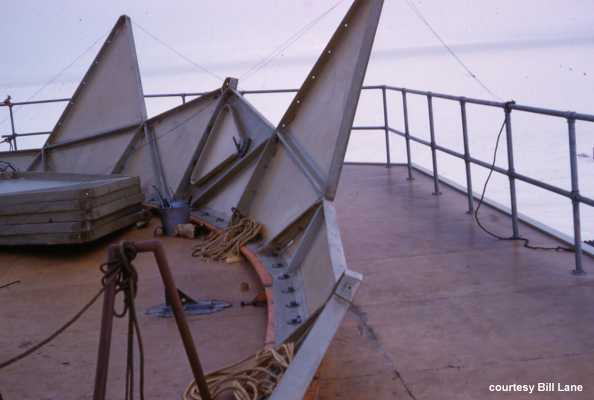
The radome is under construction.
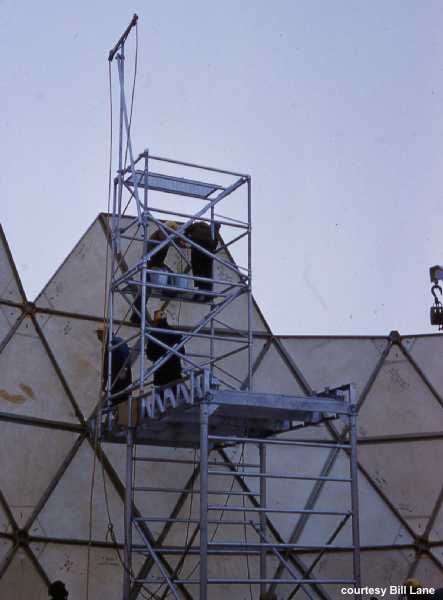
The radome is under construction.
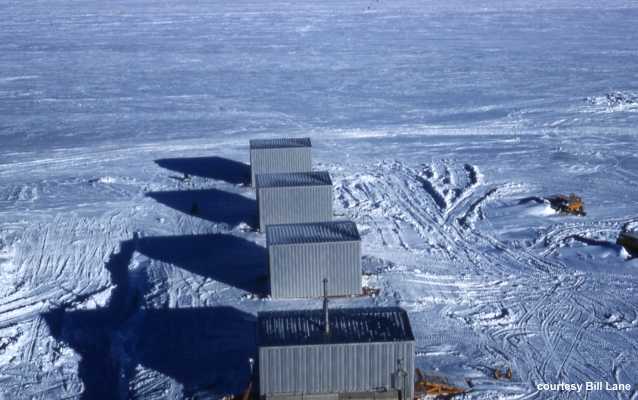
The outbuildings are compete.
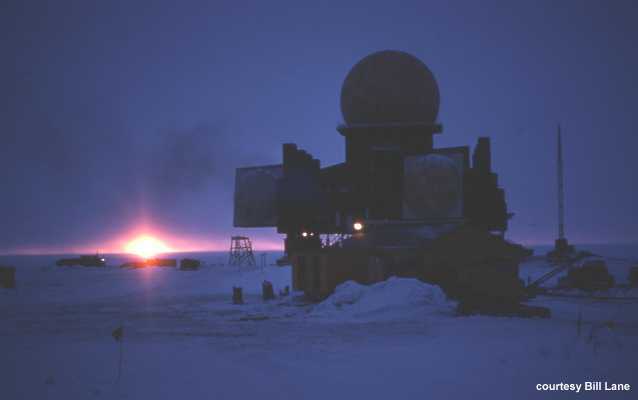
November, the building is complete.
These photos show the four P.O.L. storage tanks at various stages of construction.
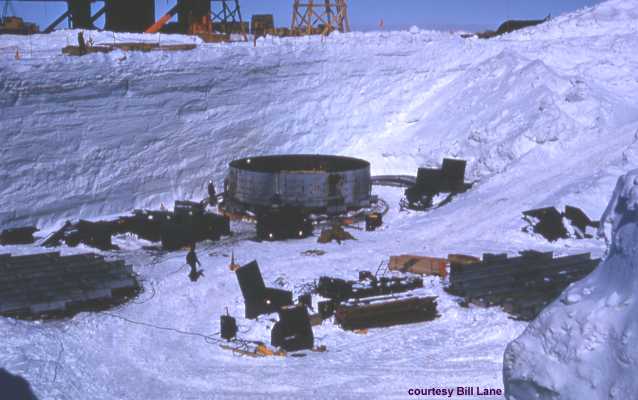
Early stages of construction. Note that the tank’s steel grillage is founded on a heavy timber mat.

Back filling of the four P.O.L. storage tanks is about to begin.
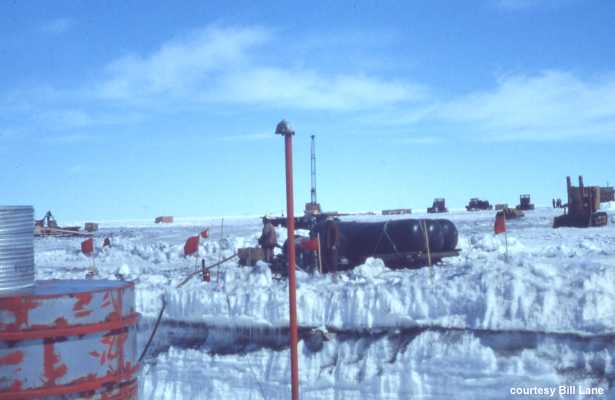
A P.O.L. storage tank is being filled with fuel. Note the rubber bladders on the sled. Also note the dark area in the face of the excavation which was grade at the end of the 1959 construction season.
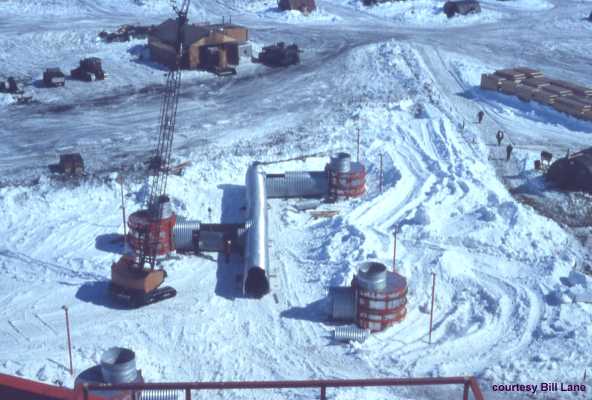
The corrugated metal pipe tunnel between the tanks is 50% complete.
These photos give an idea of life at the Dye 2 site during the construction phase. The construction workers worked 10 hours a day 7 days a week.
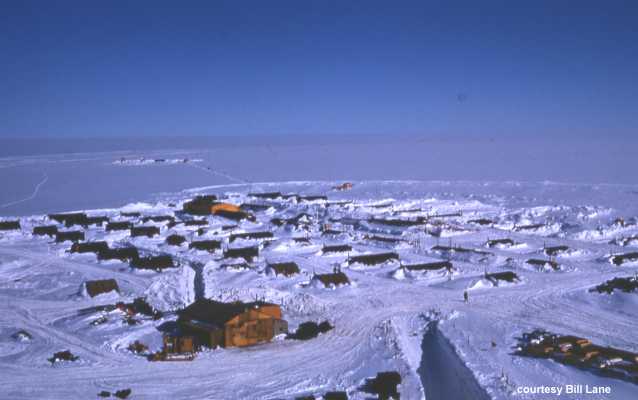
The temporary camp. This photo was taken from the top deck of the main building.

During the summer it was necessary to haul snow into the camp.
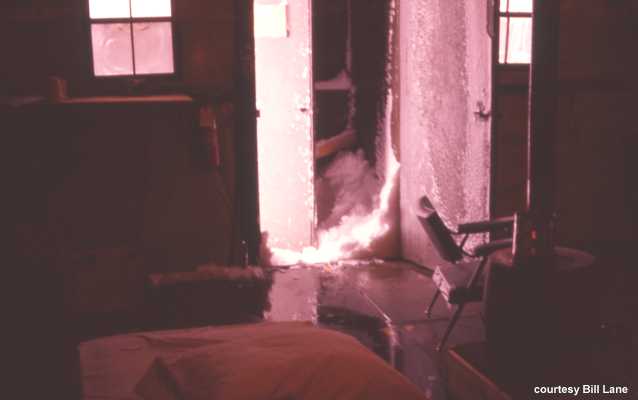
Looking out the door of a Jamesway hut after a heavy snow.